about Nickel electroplating
Nickel is plated for many reasons. First and foremost, nickel provides a decorative appearance because of its ability to cover imperfections in the basis metal (leveling). Nickel deposits can be made brilliant, and when covered by a thin layer of decorative chromium, will maintain their brilliance even under severe conditions. Satin nickel under bright or dark chromium offers a wide range of decorative appearances. When multi-layers of nickel are applied, excellent corrosion protection can also be achieved. This requires plating two (duplex) or more different kinds of nickel (semi-bright and bright nickel for duplex; high-potential and particle nickel).
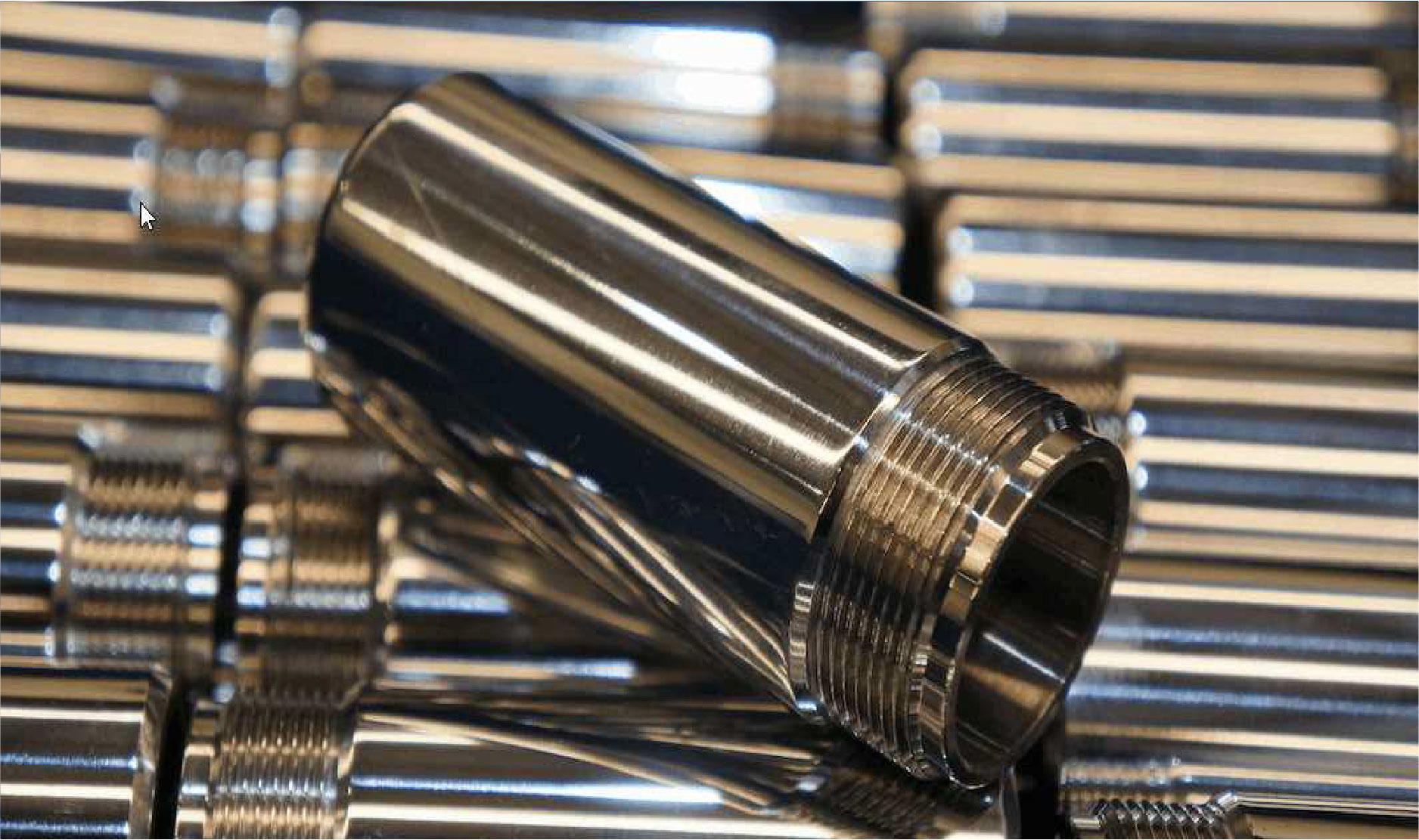
Nickel deposits also offer more wear resistance than softer metals such as copper or zinc, and thus can be used when wear resistance is needed. Because nickel is magnetic, it can sometimes be plated where the ability to be magnetized is needed. Finally, nickel can be made to plate with little or no stress and is therefore used for electroforming or aerospace applications where stress needs to be held to a minimum. Depending on the application, many of these requirements are specified simultaneously, so that nickel is often plated for more than just one reason.
Why Apply Nickel Plating?
Nickel Plating is done for several reasons, including:
- Strengthening metals against rust and other forms of corrosion
- Protecting lightweight plastics from wear and tear
- Adding aesthetic value to a dull appearance
- Increasing the hardness of the underlying surface
- Adding resistance for alkaline environments
- RFI/EMI shielding
Nickel plating is also a powerful option for aerospace and defense engineers looking to prevent atmospheric corrosion. A zinc-nickel coating acts as a “sacrificial layer” that absorbs the corrosive materials before they can get through the aircraft or other machinery, and potentially weaken it structurally.